Cleaning and drying
Sink Float Tank
Type: WSST
The WIPA Frictionwasher/separator type FW is used for intensive washing, but also for dewatering plastics.
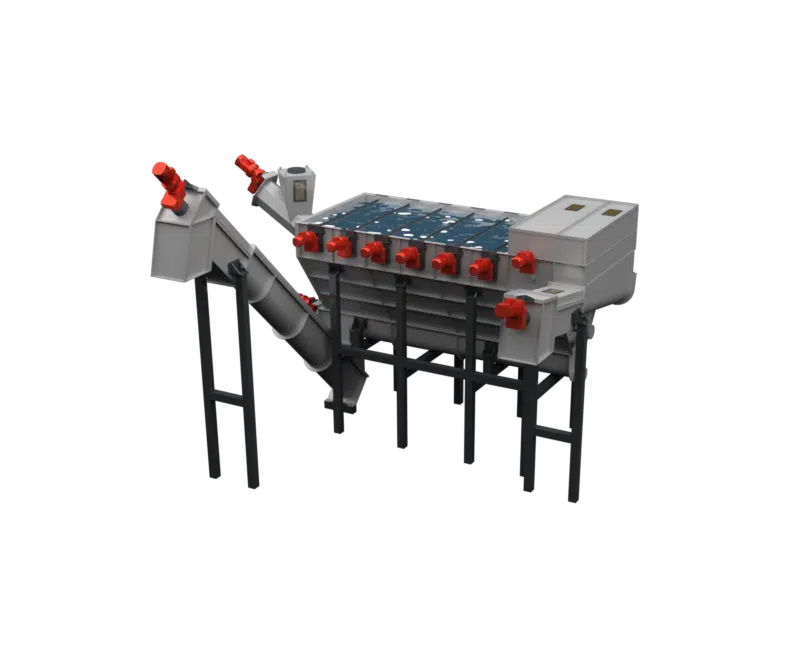
Sink Float Tank
The process
Explanation using the example of PP/PE separation in PET bottle recycling: The pre-shredded material is fed into the separation tank via 2 screws below the water surfaces. As PET is heavier than water, it sinks to the discharge unit for the sediment and is conveyed out of the machine by a screw or scraper chain conveyor. PP and PE, on the other hand, rise to the surface of the water and are conveyed to the floating material discharge by various paddle drums connected in series and pressed under water several times in order to separate any PET that may still be adhering. A Frictionwasher is usually installed downstream of a separation tank, as this can separate large quantities of liquid from the material.
MODULAR
The WIPA separation tanks of type WSST are available in various sizes and, thanks to their modular, expandable design, can also be adapted to larger or smaller throughput capacities after installation.
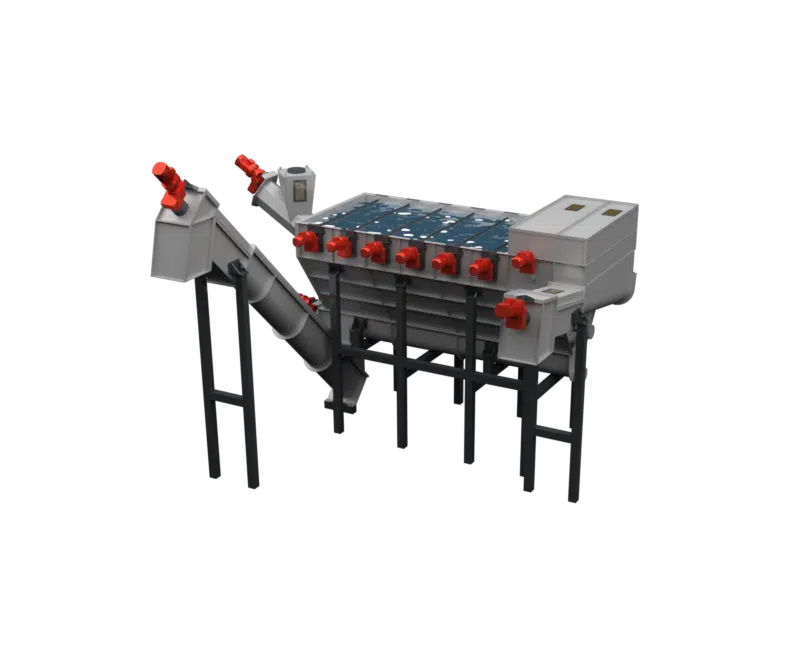
See for yourself:
This machine offers these advantages
- Effective separation of different specific densities
- Expandable and adaptable to e.g. throughput rate and material thanks to modular design
- Dosing unit for adjusting the density of the water with e.g. salt optionally available
- Elements can be easily replaced if the material is changed or damaged
- Various discharge systems for a wide range of contaminants
- Compact, efficient design
The Sink Float Tank in 360
All data at a glance
Technical data | WSST 1500 | WSST 2000 | WSST 2500 |
Number of paddles | 2 / 4 / 6 /8 | 2 / 4 / 6 /8 | 2 / 4 / 6 /8 |
Paddle drive in kW | 0,75 | 0,75 | 0,75 |
Discharge drive | 0,75 | 0,75 | 0,75 |
Throughput capacity up to | t/h | t/h | t/h |
LDPE film | 1 | 1,5 | 2 |
PP regrind/PET bottle flakes | 4,5 | 6 | 8 |
Throughput rates and technical data are based on experience and may vary depending on the material.